In the first part of our three-part series on "Demystifying Cost Accounting: Beyond the Numbers," we...
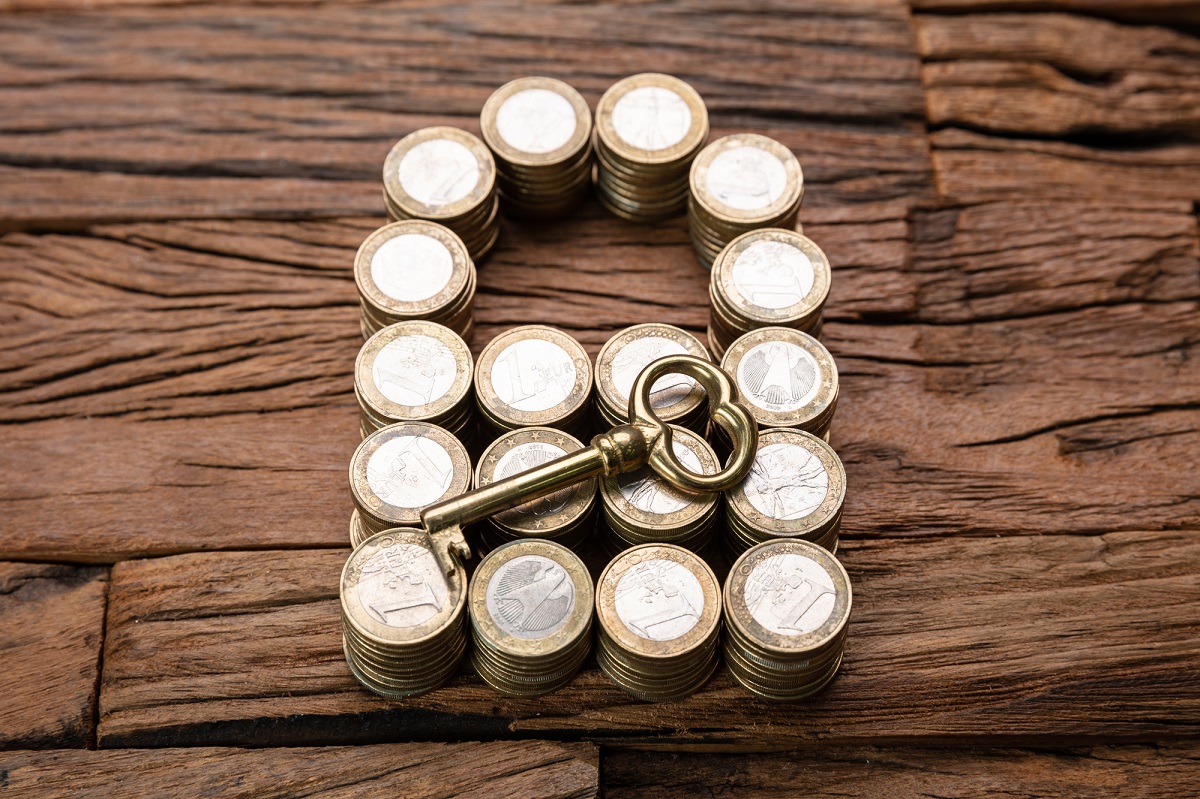
Effective cost control is vital for manufacturing businesses seeking to enhance profitability and competitiveness. In the second part of our blog series, we focus on the practical aspects of cost control in manufacturing. This article is designed to provide CFOs with actionable strategies for optimising manufacturing costs, harnessing technology for cost management, and implementing effective budgeting techniques.
Techniques for Cost Control in Manufacturing
- Lean Manufacturing: This approach identifies and eliminates non-value-adding activities, optimises resource utilisation and reduces costs.
- Just-In-Time (JIT) Inventory: This strategy minimises inventory holding costs by aligning raw material orders from suppliers directly with production schedules.
- Total Quality Management (TQM): TQM reduces costs associated with rework, waste, and returns by focusing on quality improvement.
- Outsourcing Non-Core Activities: Companies can lower costs by outsourcing non-essential functions such as maintenance or certain administrative tasks to specialised firms.
- Energy Efficiency Measures: Implementing energy-efficient practices and machinery can significantly reduce utility costs, which are a major expense in manufacturing.
The Role of Technology in Cost Tracking and Variance Analysis
Advancements in technology play a crucial role in cost control:
- Automated Tracking Systems: They can provide real-time data on production costs, enabling quick identification of overruns.
- Data Analytics and Artificial Intelligence (AI): These tools can predict trends, identify inefficiencies, and suggest improvements.
- ERP Systems: Enterprise Resource Planning systems integrate various business processes, offering a comprehensive view of costs and aiding in efficient resource allocation.
Budgeting for Manufacturing: How to Forecast and Manage Costs Effectively
- Zero-Based Budgeting (ZBB): This method involves building the budget from scratch each year, justifying each expense, and aligning them with business objectives.
- Flexible Budgeting: Adaptable to changes in production levels, flexible budgeting is essential in industries where demand is unpredictable.
- Variance Analysis: Regular variance analysis between actual and budgeted costs helps identify and address discrepancies in a timely manner.
- Rolling Forecasts: This approach allows continuous updating of budget forecasts based on current business trends and market conditions.
Why Costing in Manufacturing Is Important
Costing in manufacturing is not just a routine accounting exercise; it's a critical business function that impacts various facets of a company's operations and Strategic Planning. This section highlights why accurate costing is indispensable in manufacturing, from setting the right prices to fostering financial health and supporting strategic decisions.
Informed Pricing
- Accurate Cost Recovery: Proper costing ensures that all direct and indirect expenses are accounted for in the product's price. This is crucial for recovering costs fully and avoiding losses.
- Competitive Pricing: Understanding the cost structure allows businesses to price their products competitively without sacrificing margins.
- Profitability Assurance: By accurately incorporating all costs, companies can set prices that not only cover expenses but also ensure desired profit margins.
Budget Management
- Effective Budget Allocation: Accurate costing provides a clear picture of where and how resources are utilised, allowing for more effective budget allocation.
- Cost Overrun Prevention: With detailed cost insights, companies can identify potential areas of overspending and take corrective action before significant overruns occur.
- Cost Reduction Identification: Regular cost analysis helps pinpoint areas where efficiencies can be improved and costs can be cut without impacting product quality.
Financial Health
- Accurate Financial Reporting: Proper costing leads to more accurate financial statements, reflecting the true financial status of the company.
- Investor and Lender Confidence: Investors and creditors often look at cost management as an indicator of a company's financial prudence and stability, influencing their confidence and decisions.
- Creditworthiness and Funding: Companies with well-managed costs and accurate financial reporting are more likely to be viewed favourably by lenders and investors, facilitating further access to capital and credit.
Strategic Planning
- Insightful Profit Analysis: Businesses can make informed decisions about where to focus their efforts by understanding which products or services are most profitable.
- Resource Allocation Optimisation: Cost analysis provides valuable insights into the most efficient use of resources, guiding strategic decisions about production, investment, and expansion.
- Long-Term Planning Support: Accurate costing helps with forecasting and long-term planning by providing reliable data on cost trends and profitability.
Effective costing in manufacturing is a cornerstone of sound financial management. It plays a vital role in pricing, budgeting, maintaining financial health, and guiding strategic business decisions, ultimately driving the success and sustainability of manufacturing enterprises.
Benefits of Effective Costing in Manufacturing
Costing serves as a foundational element for strategic business management. This section explores the substantial benefits of effective costing practices, including enhanced profit margins, gaining a competitive advantage, and boosting operational efficiency.
Enhanced Profit Margins
- Accurate Cost Allocation: Effective costing ensures that all production costs are accurately allocated, providing a clear understanding of the actual manufacturing cost for each product.
- Improved Pricing Strategies: With a thorough understanding of costs, businesses can set prices that not only cover all expenses but also deliver healthier profit margins.
- Cost Reduction Opportunities: Regular and accurate costing helps identify areas where costs can be trimmed without compromising quality, directly improving the bottom line.
Competitive Advantage
- Pricing Flexibility: Detailed knowledge of cost structures enables companies to adjust pricing strategies in response to market changes, offering a significant competitive edge.
- Market Positioning: Costing insights can guide a business’s market positioning based on its cost structure and industry dynamics.
- Customer Value Optimisation: Manufacturers can optimise the value offered to customers by balancing costs and pricing, enhancing clients’ satisfaction and loyalty.
Operational Efficiency
- Informed Decision-Making: Regular cost assessments provide valuable insights for decision-making, from procurement to production planning.
- Waste Reduction: Effective costing highlights areas of waste and inefficiency, allowing businesses to streamline operations and reduce unnecessary expenses.
- Continuous Improvement: A robust costing system fosters a culture of continuous improvement, with regular reviews and updates to processes in pursuit of efficiency and cost-effectiveness.
In summary, effective costing in manufacturing is not just a tool for financial management but a strategic asset that drives profitability, competitive positioning, and operational excellence. By harnessing the power of accurate and insightful costing, manufacturing businesses can significantly improve their overall performance and market standing.
Challenges of Costing Systems in Manufacturing
While effective costing is undeniably beneficial, it's not without its challenges and downsides. This section examines the complexities, resource intensiveness, and adaptability challenges associated with implementing and maintaining costing systems in the manufacturing sector.
Complexity
- Implementation Challenges: Setting up a costing system in a diverse manufacturing environment can be complex and daunting. It often involves integrating various processes and systems, which can be technically challenging.
- Data Accuracy Concerns: The complexity of costing systems can lead to issues with data accuracy, especially if the system isn’t well-integrated or if there's a lack of understanding among the staff responsible for data input.
- Understanding and Interpretation: The complexity of data produced by these systems can also make it difficult for management to understand and interpret cost information correctly, which may lead to suboptimal decisions.
Resource-Intensive
- Time and Labour: Establishing and maintaining an accurate costing system demands significant time and labour, particularly in data collection, entry, and analysis.
- Ongoing Maintenance Cost: Besides the initial setup costs, such systems require ongoing maintenance, updates, and possibly training, which can be a substantial financial investment.
- Need for Skilled Personnel: Effective operation of these systems often requires skilled personnel with expertise in accounting and manufacturing, adding to human resource costs.
Adaptability
- Keeping Pace with Technological Changes: As production methods and technologies evolve, costing systems need to adapt accordingly. This can be a significant challenge, especially for smaller businesses with limited resources.
- Flexibility Requirements: The system must be flexible enough to accommodate changes in product lines, production volumes, and operational methodologies.
- Risk of Obsolescence: There’s a risk that a costing system might become obsolete if it fails to adapt to changes in the industry, market, or technology, leading to inaccurate cost data and misguided decision-making.
Applying Cost Accounting
A software company develops custom solutions for clients. Cost accounting helps determine the cost of each project by tracking the time developers spend and the overhead costs. This information is crucial for pricing services and ensuring profitability. Another example is an entrepreneur who wants to start a new eco-friendly apparel line. They use cost accounting to calculate the break-even point when the total costs equal total revenue. This analysis helps understand how many units need to be sold at a particular price to cover costs and generate profit.
Conclusion
In summary, implementing cost control in manufacturing is a multifaceted exercise involving operational strategies, technological tools, and comprehensive budgeting techniques. By adopting these strategies, manufacturers can optimise costs, improve operational efficiency, and enhance profitability in an increasingly competitive marketplace. This part offers a comprehensive overview of strategies and considerations for implementing cost control in manufacturing. It aims to equip CFOs with the knowledge and tools to optimise costs, improve efficiency, and enhance profitability.
Part 3 of our series will provide an action plan for implementing cost accounting.
Subscribe to
FP&A Trends Digest
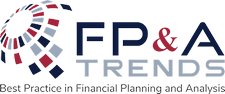
We will regularly update you on the latest trends and developments in FP&A. Take the opportunity to have articles written by finance thought leaders delivered directly to your inbox; watch compelling webinars; connect with like-minded professionals; and become a part of our global community.