Challenging market and rising costs put businesses into a non-stop race for efficiency and expense reduction...
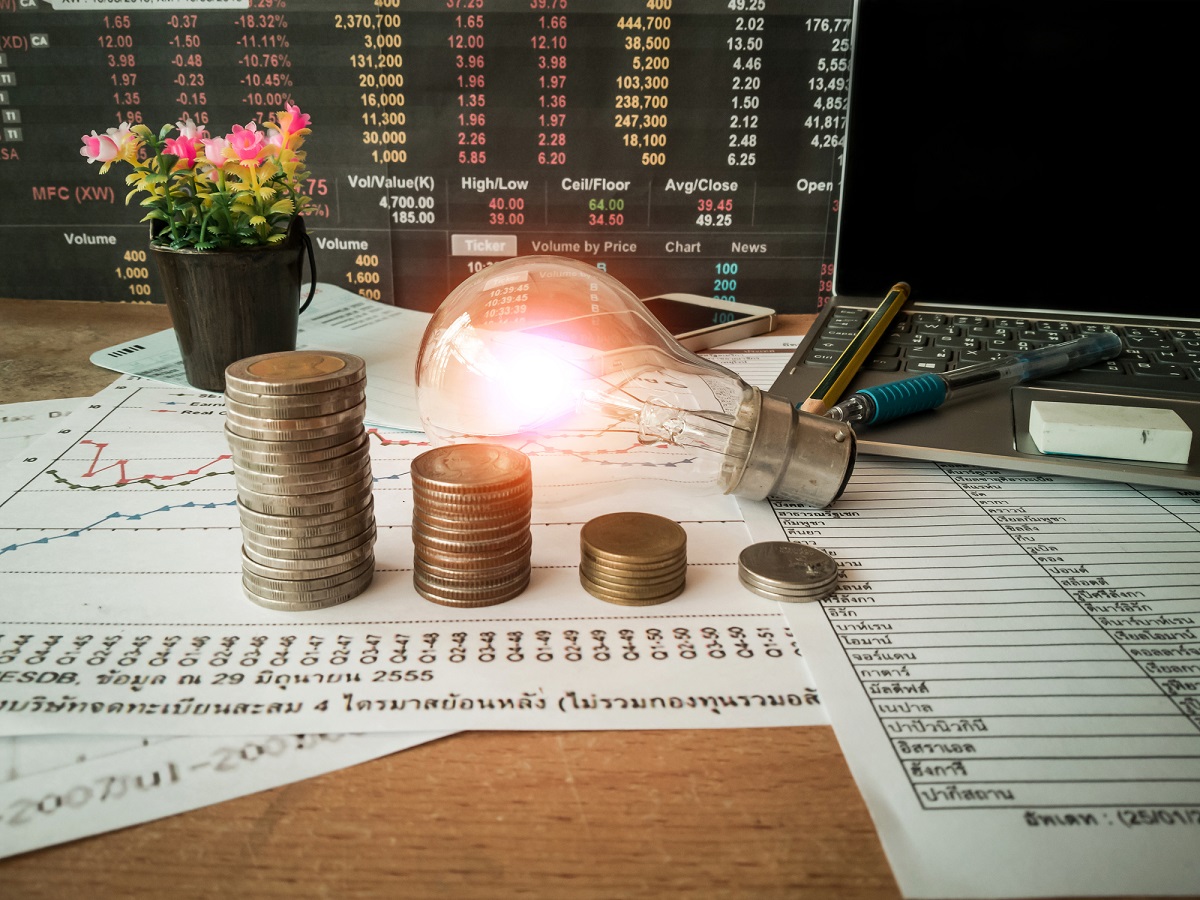
In the first part of our three-part series on "Demystifying Cost Accounting: Beyond the Numbers," we delve into manufacturing costing, an essential element often overlooked in business management. This series aims to enlighten fellow CFOs on the strategic significance of cost accounting.
In the intricate tapestry of business management, cost accounting often finds itself relegated to the background – a misunderstood element shrouded in the myth of mere expense management. However, it's time to challenge this perception.
Contrary to popular belief, cost accounting transcends the simplistic goal of cost-cutting. It's an analytical tool that empowers finance leaders to understand the true value of every facet of their operation. By demystifying this concept, we can shift the focus from viewing cost accounting as a compliance necessity to recognising it as a crucial tool for navigating business decisions.
The myth surrounding cost accounting paints it as a back-office function, overshadowed by the more glamorous aspects of business strategy. Yet, it is a dynamic ally in the journey toward sustainable growth and efficiency. Effective cost accounting doesn't just track expenses; it illuminates pathways for strategic decisions and growth opportunities, aligning financial insights with business objectives.
In this article, we explore how cost accounting can be leveraged not as a ledger confined to numbers but as a strategic resource.
Introduction to Manufacturing Costing – the Backbone of Financial Decision-Making
Manufacturing costing is more than a mere calculation; it's the backbone of strategic financial decision-making in any mass production business. This part of the series delves deep into the basics of manufacturing costs, their classification, and their pivotal role in shaping pricing strategies and analysing profitability.
Understanding the Basics of Manufacturing Costs
At its core, manufacturing costing involves determining the total cost incurred to produce a product. This process is fundamental for businesses to not only price their products effectively but also to understand and streamline their manufacturing processes. The costs associated with manufacturing can be direct or indirect and vary significantly depending on the nature of the business, the complexity of the production processes, and the scale of operations.
Classification of Manufacturing Costs
Manufacturing costs can be broadly classified into three categories:
Direct Materials
These are the raw materials that can be directly attributed to the production of a specific product. For example, timber used in furniture making or steel in car manufacturing. Effective direct materials management is crucial as they represent a significant portion of total costs.
Direct Labour
This refers to the wages paid to workers directly involved in production. It includes the labour cost to convert raw materials into finished products, like the wages paid to machine operators or assembly line workers.
Manufacturing Overhead
The most complex category, manufacturing overhead, often encompasses all the costs associated with production that cannot be directly tied to a specific product. It includes indirect materials like lubricants and cleaning supplies, indirect labour such as maintenance staff and supervisors, and other overhead costs, such as factory rents, utilities, and equipment depreciation.
The Role of Costing in Pricing Strategy and Profitability Analysis
Understanding manufacturing costs is pivotal in developing an effective pricing strategy. It ensures that the price set for products covers the costs and generates a reasonable profit. This process involves carefully considering various factors, including market demand, competition, and customer value perception.
Profitability Analysis, another critical aspect, relies heavily on accurate manufacturing costing. Businesses can identify areas where they can reduce costs, improve efficiency, and increase profitability by analysing the cost structure. This analysis also helps make informed decisions about product mix, scaling production, and investing in new technologies or processes.
In summary, manufacturing costing is not just about numbers; it's a strategic tool that underpins many crucial business decisions. A comprehensive understanding of manufacturing costs leads to more informed pricing strategies and deeper Profitability Analysis, ultimately guiding a business towards financial success.
Costing Methodologies – Choosing the Right One for Your Business
Selecting an appropriate costing methodology is a critical decision for businesses, impacting everything from financial reporting to Strategic Planning.
Overview of Different Costing Methods
Job Order Costing
Ideal for businesses where products or services are customised, job order costing tracks costs for each job or order. This method offers detailed cost tracking, which is crucial in industries like construction, custom manufacturing, or specialised services.
Process Costing
Used when products are more homogeneous and produced continuously, such as in chemical, food, or petroleum industries. Process costing accumulates costs for a period and then allocates them evenly across all units produced, offering a simplified view of costs per unit.
Activity-Based Costing (ABC)
This method assigns costs to products based on the activities required to produce them. ABC is particularly useful in complex environments where indirect costs are significant. It helps identify non-value-adding activities, making it popular in manufacturing and services industries with diverse product lines.
Standard Costing
This involves assigning a fixed cost to each production component based on historical data. It's useful for budgeting and variance analysis. Standard costing is widely used in industries with stable production processes, such as mass manufacturing.
Application of Costing Methods in Different Industries
Through real-world examples, we'll see how different industries apply these costing methodologies. For instance, a custom furniture manufacturer uses job order costing to determine the cost of each piece of furniture precisely, or a petroleum company employs process costing to allocate costs across thousands of gallons of oil. Another example is a manufacturing business that produces several products and wants to identify the cost of each product to determine pricing and profitability. Cost accounting helps allocate the indirect costs (like electricity, rent, and salaries) to each product line based on direct labour or machine hours used.
Impact of Costing Methodology on Financial Statements and Business Decisions
The choice of costing methodology significantly influences how costs are recorded and reported in financial statements. In turn, it affects Key Performance Indicators (KPIs) like gross margin, operating income, and net profit. The methodology chosen can also provide insights for strategic decisions, such as pricing, budgeting, and identifying areas for cost reduction.
For example, a company using activity-based costing might discover that certain activities or processes are more costly than previously anticipated, leading to decisions aimed at streamlining or automating those processes.
Conclusion
In conclusion, this first part of our series establishes the foundational understanding of manufacturing costing and its strategic importance in business decision-making. We will further explore the intricate dynamics of cost accounting and strategies to optimise manufacturing costs.
Subscribe to
FP&A Trends Digest
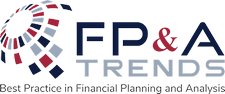
We will regularly update you on the latest trends and developments in FP&A. Take the opportunity to have articles written by finance thought leaders delivered directly to your inbox; watch compelling webinars; connect with like-minded professionals; and become a part of our global community.