Many millions of people are stuck with the habit of smoking. They know its bad for...
One day in November, a worried operations manager for a transport company was preparing for a meeting with the group’s financial director. He’d been ordered to explain the overspending on his region’s fuel account for the first 10 months of the financial year. The variance was huge and the MD had hit the roof!
Fuel budget – 10 months to end of October $5,000,000
Fuel actual – 10 months to end of October $8,000,000
Negative variance ($3,000,000)
There were many reasons for the variance. The operations manager’s explanations were as follows:
1. Price
“At budget time we thought the fuel price would remain steady at $4.00 per litre, but it quickly went up and is now $6.00 per litre.”
2. Volume
“At budget time we didn’t know whether our company would be awarded the National Sugar contract. I couldn’t budget for it because the tender was still being adjudicated. We were awarded the contract in February, so we’ve consumed a great deal of additional fuel”
3. Mix
“Company policy has always been to use diesel-driven vehicles in our fleet, but for the National Sugar contract, our technical people advised us to buy petrol-driven vehicles. Petrol is about 50% more expensive than diesel.”
4. Timing/calendar/smoothing
“Our new depot has just become operational and we needed to fill the new 20,000-litre tank. I budgeted for this to happen in November; in fact, the new tank became operative in October.”
5. Waste, loss and inefficiency
“Two vehicles collided with each other in our yard and caught alight. The insurance company alleges negligence and refuses to settle. Also, an underground pipe in our main depot sprang a leak and we lost 10,000 litres of fuel. Finally, a ring of employees was falsifying petrol purchases at a filling station on one of our routes”.
The group financial director listened to the manager’s nervous explanations and sighed to himself. He wondered how many meetings like this he’d have to attend, year after year, where good managers, like his colleague today, trotted out the same old excuses for their overspending.
In the financial director’s opinion, the explanations for the first four variances added very little value to the conversation. They are “assumption variances” explaining that the assumptions and guesses made at budget time were not what happened in reality. The only really important item in this meeting, in his opinion, was the fifth variance, which focuses on waste, loss and inefficiency.
The financial director knew that the Board was considering his proposal to move from annual fixed budgets to rolling forecasts. If the proposal was adopted, the operations managers in the group would be required to forecast their monthly fuel expenditure in litres, and submit their forecasts for approval to their regional manager. At month or quarter-end, actual spend would be reported against this forecast, not against a budget set ten months ago. And in this instance, the financial director thought to himself:
- The manager’s forecast would be based on the ruling fuel price.
- The National Sugar contract volumes would be incorporated.
- He would take the policy change from diesel to petrol into account.
- The timing of the new depot’s fuel purchase would be correct.
And any variance reported against this forecast at the end of the month would arise almost entirely from waste and inefficiency, the fifth variance, which is what management should be focussing on in the first place!
The article was first published in Unit 4 Prevero Blog
Subscribe to
FP&A Trends Digest
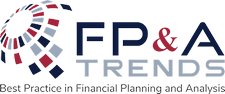
We will regularly update you on the latest trends and developments in FP&A. Take the opportunity to have articles written by finance thought leaders delivered directly to your inbox; watch compelling webinars; connect with like-minded professionals; and become a part of our global community.